
The profile-milling sequence can also be simulated (e.g., in Vericut shown in Figure 2.11b). CAD/CAM will generate a toolpath like that shown Figure 2.11a the toolpath wascreated using Pro/MFG for this example. At this point, a machining sequence iscompletely defined. In the meantime, users choose a cutter andspecify machining parameters (e.g., federate, spindle speed). Then, users createa machining sequence (e.g., a profile-milling sequence). After the solid models are assembled, users define manufacturing set up, including choosinga workcell (e.g., a 3-axis mill) and coordinate system (or machine zero). For example, the design model and workpiece of the profile milling discussed beforeare assembled, as shown in Figure 2.11a. Theprocess starts with creating a reference (or design) model and workpiece, and then assembling them inassembly mode.
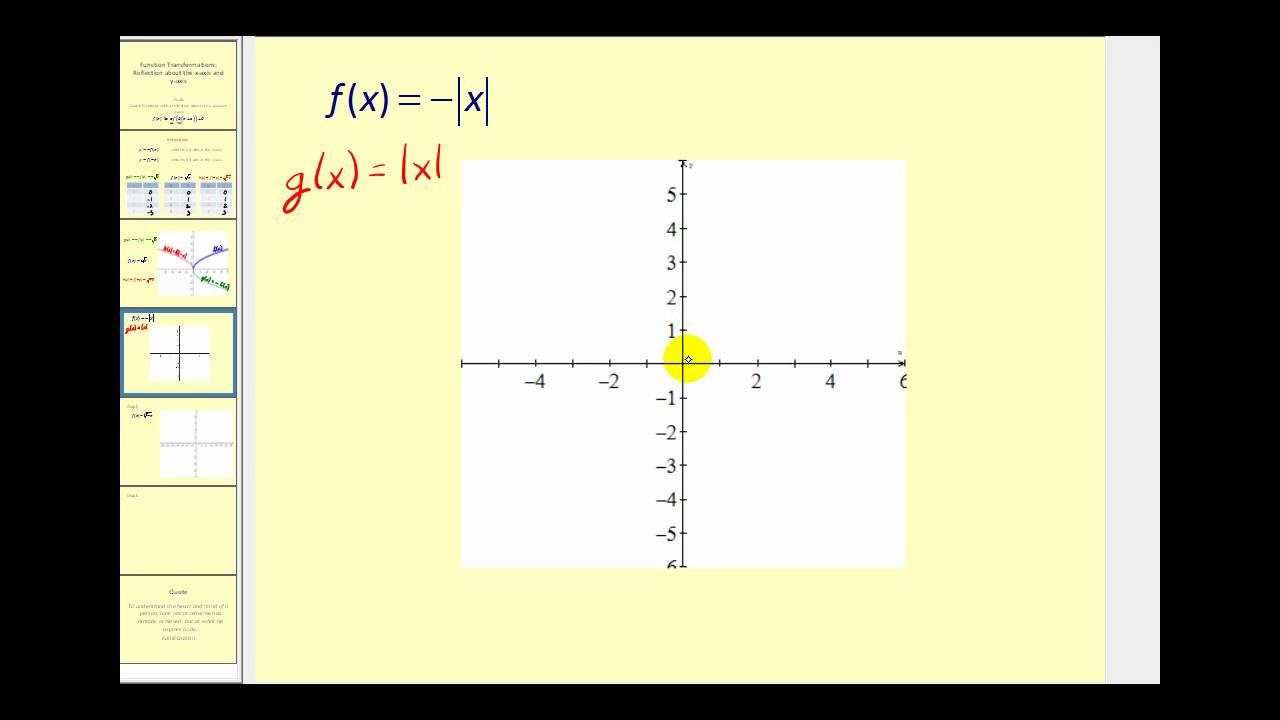
Auxiliary statements, such as COOLNT ON (turn on coolant), FEDRAT (feedrate),SPINDL (spindle speed), are also specified.2.2.4 CAD/CAM ApproachThe CAD/CAM approach is the most popular and advanced approach in generating CNC codes. 2.3 Virtual Machining Simulations 51(rapid retract).
